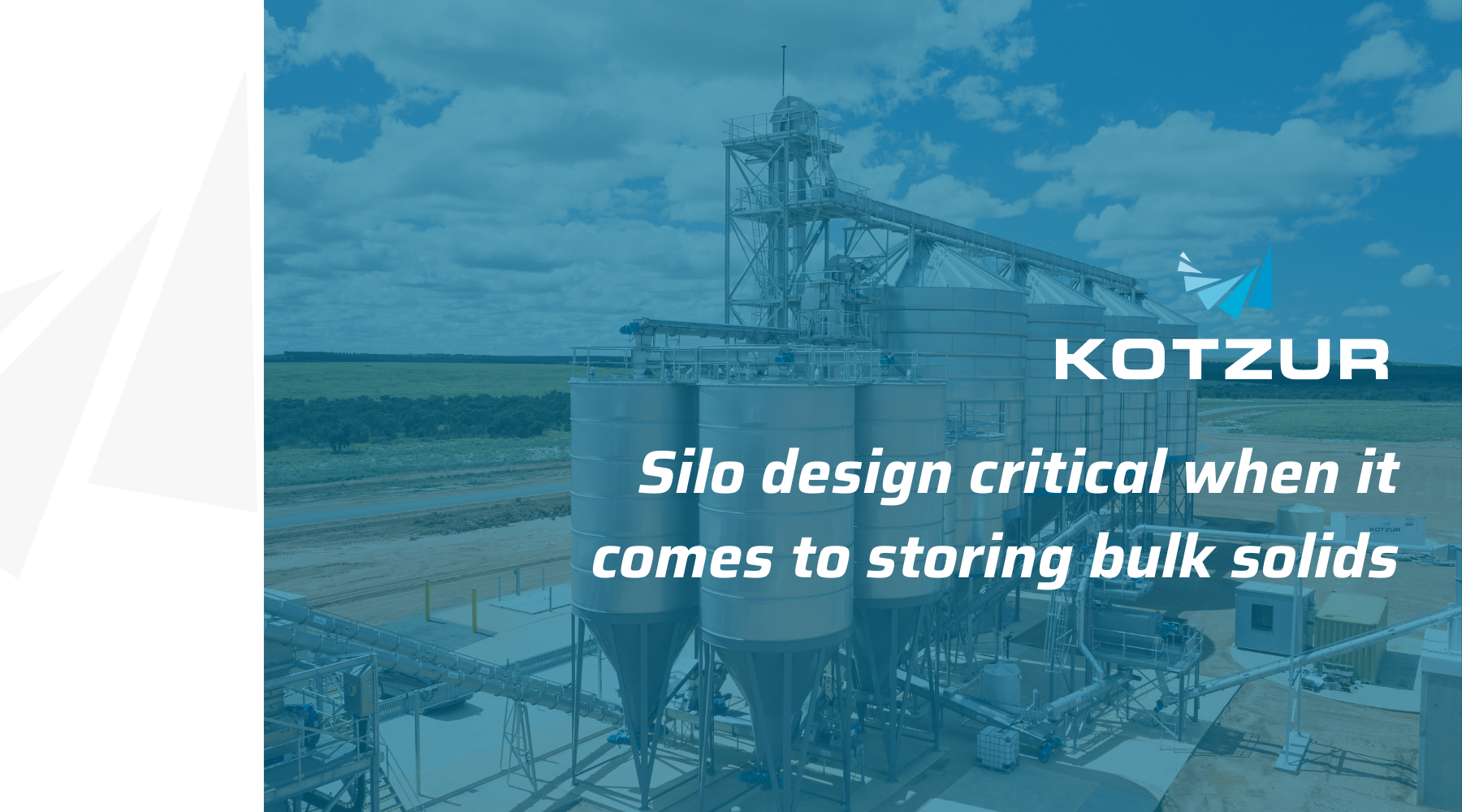
Silo design critical when it comes to storing bulk solids
Kotzur understands that one size does not fit all when it comes to silo design. Silos have a very important, yet simple job in a bulk solids handling operation – store material for later use.
If a silo isn’t fit for that purpose, it can cause all kinds of operational issues. For example, if a silo is not designed with the material’s bulk density in mind, it can lead to structural issues. This can lead to disaster, causing the structural supports to fail, or the bottom of the silo could tear away and fall out.
Ben Kotzur, Chief Technical Officer at Kotzur, said friction also plays a key role. “The critical difference between bulk solids silos and bulk liquid tanks, is that solids can carry a shear load. The material sits against the walls of the silo and puts a vertical load into the wall,” he said. “Also, if the internal friction parameters aren’t understood correctly, it can lead to anything from ratholing to mechanical arching. The material just doesn’t flow, and the silo becomes inoperable.”
Moisture also plays an important role in silo design. If a product goes in moist and dries out or vice versa, the material parameters can change drastically to the point where it will no longer flow. Corrosion can also take its toll on silos, eating through the structure and weakening it. “A silo is not a simple structure – it’s a sophisticated piece of equipment that needs to fit the client’s needs,” Kotzur said.
“When we design our silos, there are two main factors – the product being stored and the operational requirements. If you take fertiliser, for example, it needs to be maintained very dry and will cake when too much moisture gets into the product, so the aim is to protect against moisture.

“For mode of use, we look at how quickly the silo needs to be emptied. Does the process require metering? What is the desired flow rate and accuracy? What are the wind and seismic loading requirements? Is the silo subject to a corrosive environment? These affect both the silo and the systems that sit around it.”
Kotzur has a 70-year history of designing, engineering, manufacturing and delivering industrial equipment in Australia. The family-owned company, founded in Walla Walla, NSW, has expanded significantly, with facilities in Toowoomba and Perth.
Kotzur said the team believes that every bulk material and engineering challenge can be resolved – it’s just about finding the right solution. “Our range of custom silos highlights this. It’s not a one-size-fits-all situation – we ensure the glove fits the hand.”
Pellet silos
One of the common custom silos that Kotzur manufactures are designed for pellet storage. Maintaining the quality of the product is one of the highest priorities, which means keeping the material cool and dry, which also controls the risk of self-combustion for some pellet types.
Tempering silos
Tempering silos are used to help increase the moisture content of grains, meaning there is a mixture of grain and free water. Kotzur said that an important part of the process is accounting for swelling loads during the tempering process, which needs to be done during the design phase. “Not only that, but the mixture of grain and water promotes microbial activity, which in turn creates a corrosive environment,” he said.
Powder silos
Powders can be tricky to handle, which makes understanding the material properties even more important. One example of this is the compressibility of the powder – how the material can increase in density under its own weight. In large silos, these compressive loads can increase the overall density of the material quite significantly. In addition, some powders need to be kept dry to ensure they will reliably flow. They also may need to use a screw feeder and appropriately designed hopper arrangement.
Design and engineering
To ensure its silos are fit for purpose, Kotzur spends a significant amount of effort at the start of the process to learn about the material being stored. The engineering team will work with the sales team and the client to create a preliminary design of the silo, allowing the client to provide feedback. By the time the company is ready with the price and delivery time estimates, its team has a strong understanding about what is required, and what will be included. Often this process includes analysing sample of material, site visits, and learning more about the physical makeup of the product.
Bevan Austin, Kotzur Bulk Solids National Sales Manager, said it helps prevent any surprises, and allows the company to discover any issues with the design as early as possible. We always endeavour to have the correct solution or design at the front end to ensure we are offering the best possible solution for the client.
“We also have Kotzur Maintenance Services if a client has any maintenance issues. Our record keeping is very thorough as well – even if a one-off client calls us for help with a 10-year-old silo, we can track down and provide them information easily,” he said. “Everything is designed in-house – we don’t rely on a third party for design and engineering. We don’t tend to say no to projects. If you’ve got a challenging product, it’s in our nature to think about how we can find a solution.”
As featured by ABHR - Silo design critical when it comes to storing bulk solids - Australian Bulk Handling Review